How to Introduce Safety Culture to Your Organization
Team Voxel
January 31, 2024In order to successfully introduce safety culture to your organization, you’ll need to first get buy-in from your management and leadership teams, encourage communication and feedback across the organization and get the right tools to ensure your success.
In order to successfully introduce safety culture to your organization, you’ll need to first get buy-in from your manager, encourage communication and feedback across the organization and get the right tools to ensure your success.
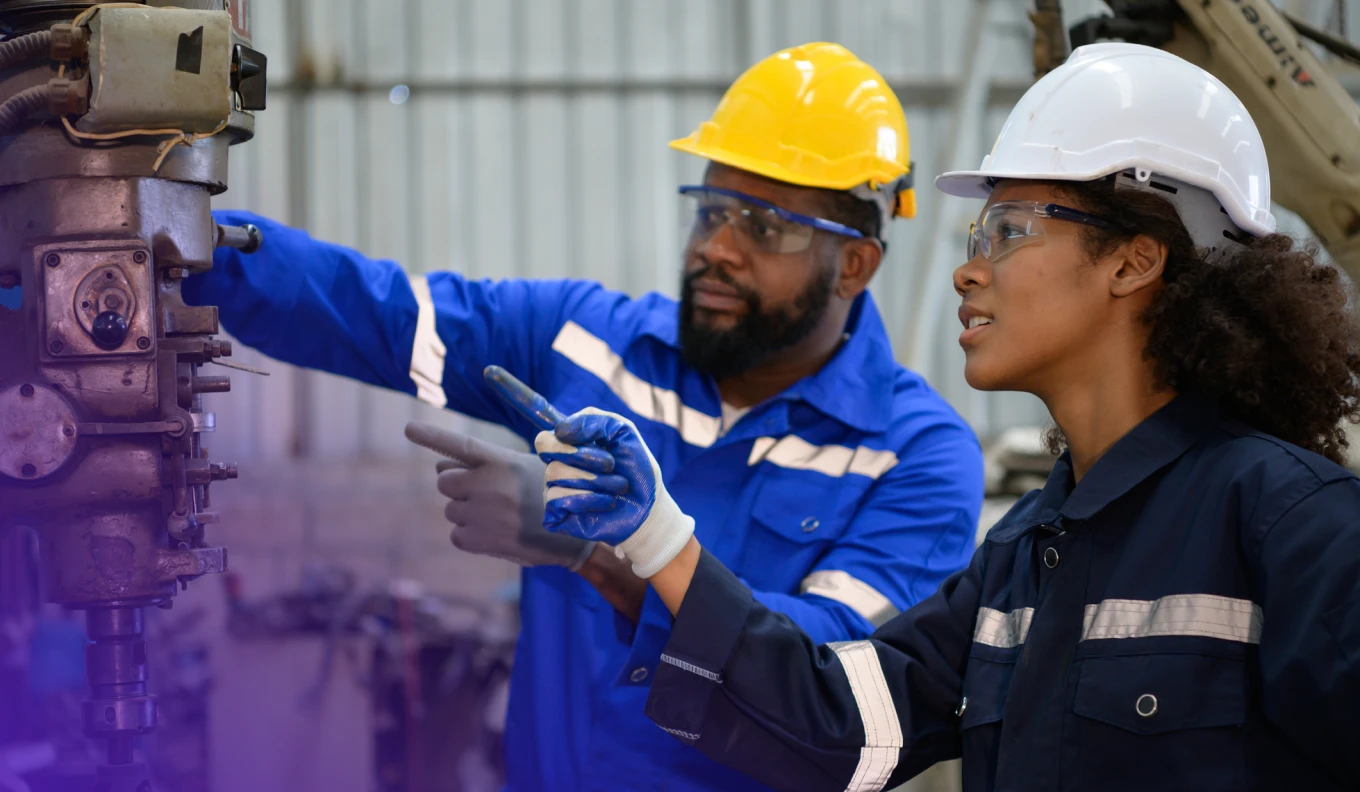
The Advisory Committee on the Safe of Nuclear Installation defines safety culture as “The product of individual and group values, attitudes, perceptions, competencies, and patterns of behavior that determine the commitment to, and the style and proficiency of, an organization’s health and safety management” With such a broad definition, it’s no wonder that it can often be challenging to get everyone on the same page.
In order to help set you up for success, here are three steps to help you successfully introduce safety culture to your organization.
- Get buy-in from managers and leadership
- Encourage communication and feedback from employees
- Find the right tools
Step 1: Get Buy-In From Managers and Leadership
Build trust with managers by highlighting benefits like time saved on incident paperwork, automation of safety compliance tasks, and potential financial savings that can be redirected towards enhancing workplace conditions and rewards.
It’s critical that everyone at the organization is bought into safety culture. Your leadership needs to understand how this changes goals and how it impacts the company’s bottom line. Managers need to understand how it changes their expectations and how to get employees on board.
The main things that we hear from managers about safety are:
- “I worry about my team being safe but I can’t be everywhere at all times to ensure that policies are followed.”
- “When an incident happens, the paperwork is such a headache.”
- “I wish there was a better way to train my team on safety procedures – it doesn’t seem like our current training is effective.”
- “The time and money we spend responding to incidents would be better spent improving our employee’s experience.”
Consistent Safety Culture Means More Productivity, Fewer Losses
With a more consistent focus on safety culture, there will be fewer incidents, which means less lost productivity, less money spent on incident-related expenses.
When talking to your leadership team about the importance of safety culture, talk about the ROI of safety. For instance, According to OSHA’s injury cost calculator, a machine crushing accident costs, on average, $57,000 in direct losses and $62,000 in indirect costs. A 2011 study at UC Davis Medical School showed that indirect costs are typically 2.7x greater than direct medical costs: if an average back injury has a direct medical cost of $25,000, the “real” cost of the injury may be closer to $90,000 or more. Keep your focus on how safety culture will help you avoid those costs, saving money for the entire organization.
Managers are also interested in productivity gains, but their focus has more to do with the manual tasks that come with incidents. Everybody hates paperwork. When an injury happens, a supervisor has to drop everything they’re doing and do an incident investigation. They have to take pictures, draw diagrams, and call a nurses’ hotline. They have to find witnesses, do interviews, write down narratives, and search for videos in the camera feed.
With a consistent focus on safety culture, they’ll have fewer incidents which leads to less paperwork, less time spent on investigations and more time to do the rest of their job.
Step 2: Get Employees Involved
After you have your leadership and management teams on board, it’s time to engage employees. You can do this with a combination of open communication channels and regular trainings focused on issues that impact them.
Open Communication For Reporting, Feedback and Suggestions
Your employees will feel empowered to participate in safety culture if they feel like they have a say in how it plays out in their day-to-day lives.
In order to do that, you need to:
- Create consistent channels for reporting safety concerns, feedback and suggestions. These should be accessible for employees and it should be clear that these concerns will be addressed in a fair, consistent manner.
- Ask for feedback as you implement changes that impact their work. Where else can we improve the safety culture? How do these changes impact their work? What can we all do better?
- Give them ownership of their work. But asking for and acting on concerns and feedback, you’re showing employees that they have ownership over safety culture just as much as you, the management or leadership teams do.
Regular Training and Coaching Tailored to Your Safety Culture
Every organization is different, and that means the training and coaching efforts will be different as well. You can tailor your training to your organization based on feedback from employees, data that illustrates areas of opportunity or trends in your industry.
A few tips for training that successfully impacts your team:
- Recognize positive behaviors as much (or more than) negative ones that need to be fixed. Tell your employees what they are doing well.
- Offer coaching as close to an incident as possible. This helps employees remember what went wrong and connect how to do better next time.
- Connect training and coaching to the value it has for your employees. Tell them how following policies will impact them.
Now that the entire organization is aligned around safety culture, it’s time to invest in the right tools to help you optimize your safety culture.
Step 3: Find the Right Tools
Safety culture is much easier and more productive with the right tools on your side.
Voxel empowers your entire organization with visibility, insights and tools to actively create a safer workplace.
You’ll be able to see the whole picture with 24/7 risk monitoring that then delivers insights like safety scores and trend reports and encourages you and your team to take action to limit incidents with smart alerts delivered straight to the Voxel mobile app.
Americold Logistics introduced Voxel as a part of their safety culture and achieved a 77% reduction in injuries in less than one year at their distribution center in Modesto, California. In addition to safety-related savings, Americold also used Voxel to mitigate a major inefficiency in their operation, tracking open doors to reduce energy costs in a temperature-controlled warehouse. The result was a direct annual savings of $1.1 million at a single warehouse site: a 2,000% direct return on their investment, before factoring the numerous indirect costs of injuries.
Key Takeaways
Introducing safety culture to your organization is no easy feat, but when you focus your efforts in the right places you’re bound to make a positive impact.
- Build trust with managers and leadership teams first by understanding their pain points and talking about how safety culture addresses their pain points
- Involve employees with feedback loops and tailored training and coaching
- Invest in the right tools that help you optimize your safety culture