Forklifts Come With Risks. Here’s How To Minimize Those Risks and Increase Operational Efficiency
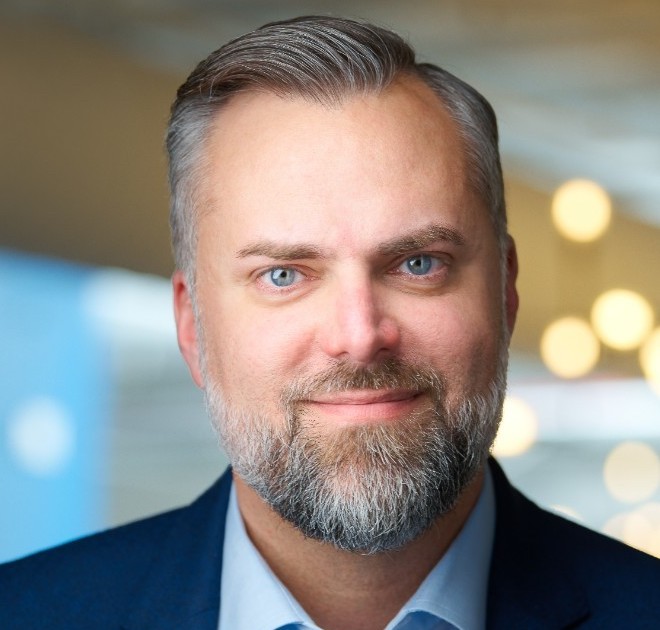
Vernon O'Donnell, CEO
January 8, 2025As companies seek safer and more efficient alternatives to forklifts, learn how Voxel is reducing risk and optimizing operations right now, with practical examples from current customers.
When people picture warehouses, forklifts zipping back and forth immediately come to mind. Warehouses, factories, and distribution centers rely on PITs (power-industrial trucks, a common acronym for forklifts in industry) to maximize productivity. And while forklifts have exponentially increased operational efficiency, they come with significant safety risks.
The Wall Street Journal recently published a story titled, “Forklifts Hurt Thousands of Workers Each Year. Factories Are Seeking Alternatives.” The article discusses manufacturers moving away from forklifts due to safety risks, citing the high financial and human cost of forklift related injuries (and, far too often, fatalities).
While going “forklift free” has appeal from a worker safety standpoint, doing so will be costly. It will take tremendous investment and a re-imagination of how facilities operate. This will not be a quick change. As Hyster-Yale Materials Handling CEO Tony Salgado is quoted in WSJ, “For the foreseeable future, manual lift trucks will be in high demand.”
So the question becomes how to markedly improve worker safety right now while warehouses and DCs are retro-fitted for a less forklift-dependent operation. We cannot afford to wait to improve working conditions. The workforce shortage continues to plague industrial-related jobs, automation is still in the early days of adoption, and the pressing need to re-establish America as an industrial power is only accelerating in today’s fraught geo-political environment.
At Voxel, we use applied AI to help companies dramatically reduce risks associated with forklifts. Our site intelligence platform leverages existing cameras to see problems previously unseen, then uses our proprietary form of AI to generate recommendations on how to make material improvements to forklift safety.
Our customers’ operational teams can quickly institute changes to risky behaviors and unsafe environmental conditions that would have previously been unknown.
Here are just a few examples from our customers:
Reduce forklift collisions and near-misses by cutting down on unsafe ‘No-Stops’
A traffic violation is a common cause of forklift accidents. Companies are neither aware of how often no-stops are happening, nor where they are occurring most frequently. Voxel uses autonomous heatmaping to help operators identify traffic patterns and problem hotspots. Ops teams can then use these tools and insights, including video clips that identify operational causes, to make changes before incidents occur.
This data-backed approach to identifying risks using leading indicators like near misses is far safer and more efficient than traditional hazard observation, which often relies on data from lagging indicators like previous collisions. Traditional observation also requires a massive commitment of resources to be effective. Voxel monitors work-floors 24/7 and pinpoints problem areas, so that operations teams can focus their resources on taking action and reducing risk.
Carlex Glass used Voxel’s autonomous heatmapping to assess their floor. They quickly installed new traffic signals and more visibly-marked pedestrian walkways to reduce incidents. In under three months, they reduced no-stops by 47%.
Alphia discovered one zone in their factory that recorded nearly 200 no-stops in less than a month after going live with Voxel. They painted the zone and added a new stop sign, which reduced the no-stops to less than two per month.
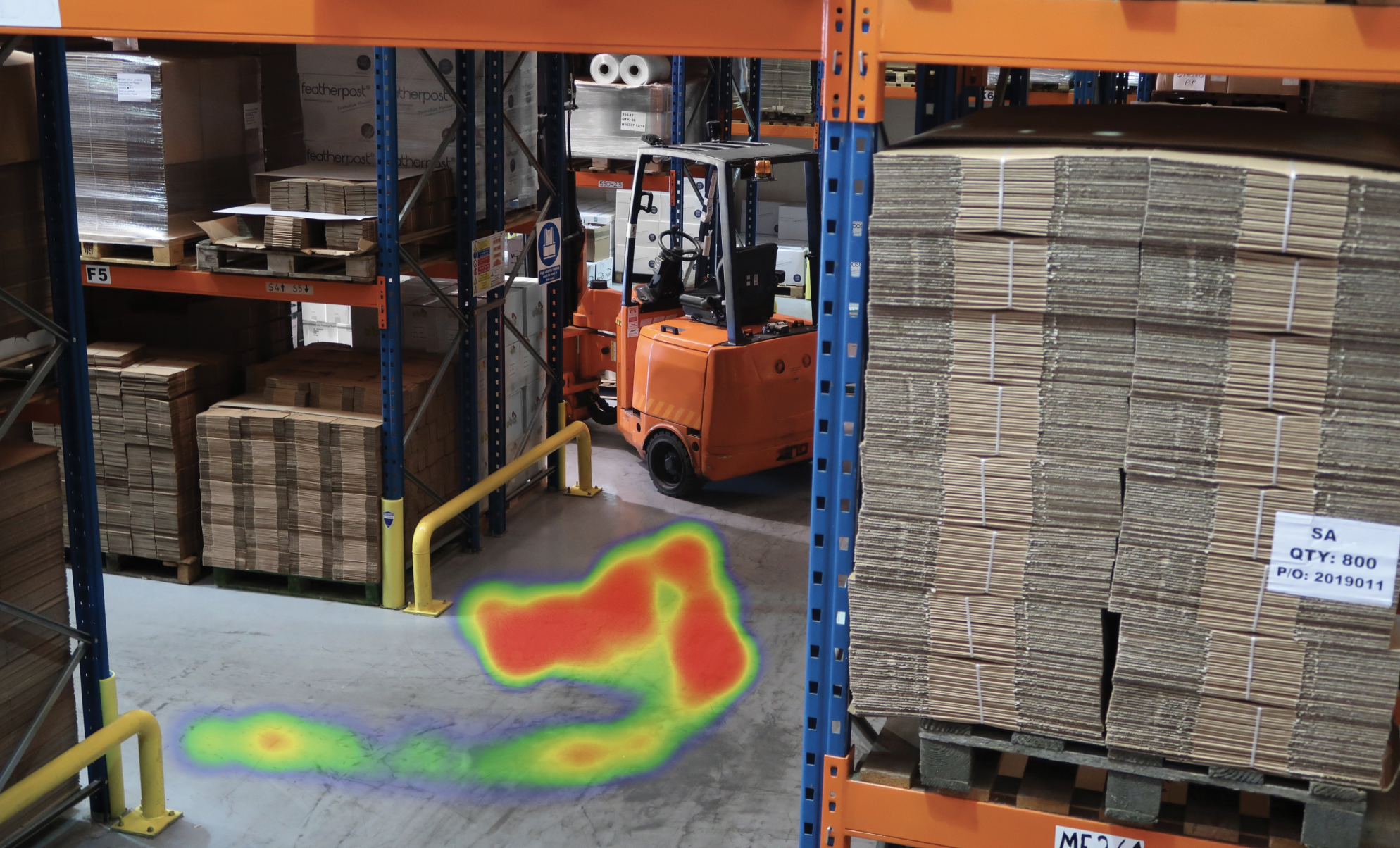
Voxel’s continuous monitoring also allows for enduring safety improvements in spite of turnover. The new traffic patterns, safer behaviors and underlying data create a new foundation for our customers’ safety culture.
Eliminate “Piggybacking” by installing faster door-closing sensors
Forklift “piggybacking” is when one forklift follows another through a door or signal, creating increased likelihood of incident occurring:
- Pedestrians or other vehicles are only expecting one forklift to come through at a time;
- The second vehicle has no time or sightline to see if its path is clear and;
- If the first vehicle has to stop short, it will likely cause a collision.
Vertical Cold Storage discovered that piggybacking was common in a few key doorways on their floor. By installing faster door-closing sensors and dedicating time to coach drivers using videos earmarked by Voxel, the VCS team reduced forklift piggybacking by 89%.
Create safer spaces via better delineated Pedestrian Zones, Vehicle Zones
It is critical to keep pedestrians and active forklifts at a safe distance from each other. Companies believe that guidelines or minimally-marked areas are sufficient, but Voxel has found consistently that pedestrians and forklifts frequently get too close when zones are not demarcated in an incredibly clear and visible fashion.
At Piston Automotive, creating “no pedestrian zones” (based on suggestions from Voxel’s algorithm) was a large part of reducing vehicle safety incidents by 86% in three months.
At Alphia, pedestrians and forklift drivers were confident that they were each leaving six feet of space between them when populating the same aisles. However, we saw that the space was frequently much smaller, leading to a high amount of “near misses.” And these close calls are highly correlated with an injury or property damage just waiting to happen. Alphia’s safety team had new pedestrian walkways installed, complete with physical barriers between those walkways and vehicle zones. This change was part of a strategy that led to a factory wide injury reduction rate of 83% in under one year.
These techniques are a few proven ways to maintain a safe workplace while continuing to heavily utilize forklifts. Every piece of equipment comes with risk. But that risk can be managed and minimized with proper monitoring, training, and policy implementation.
The necessary visibility to make these fundamental changes was out of reach before deep tech began to focus on solving these types of problems. It is why we are so passionate at Voxel about applied AI being used to solve a meaningful problem in the physical world.
We all share in the responsibility in keeping our workers safe, and we are ready to help you create that reality today. Contact Voxel to set up a demo or to find out more about how we can help.